The Process
Sustainability is extremely important to me. It plays a huge part in my production process & decision making when it comes to design.
This includes:
- Re-using off cuts - during the process the edges from pouring are removed. I save these small pieces & sort by colour, reusing again
- Failed pieces - any piece that is faulty is made into new clay
- Conscious handling of water
- Only firing when I can ensure the quality of each item will be perfect - meaning there will be no unnecessary heating
- Using recyclend paper for packaging
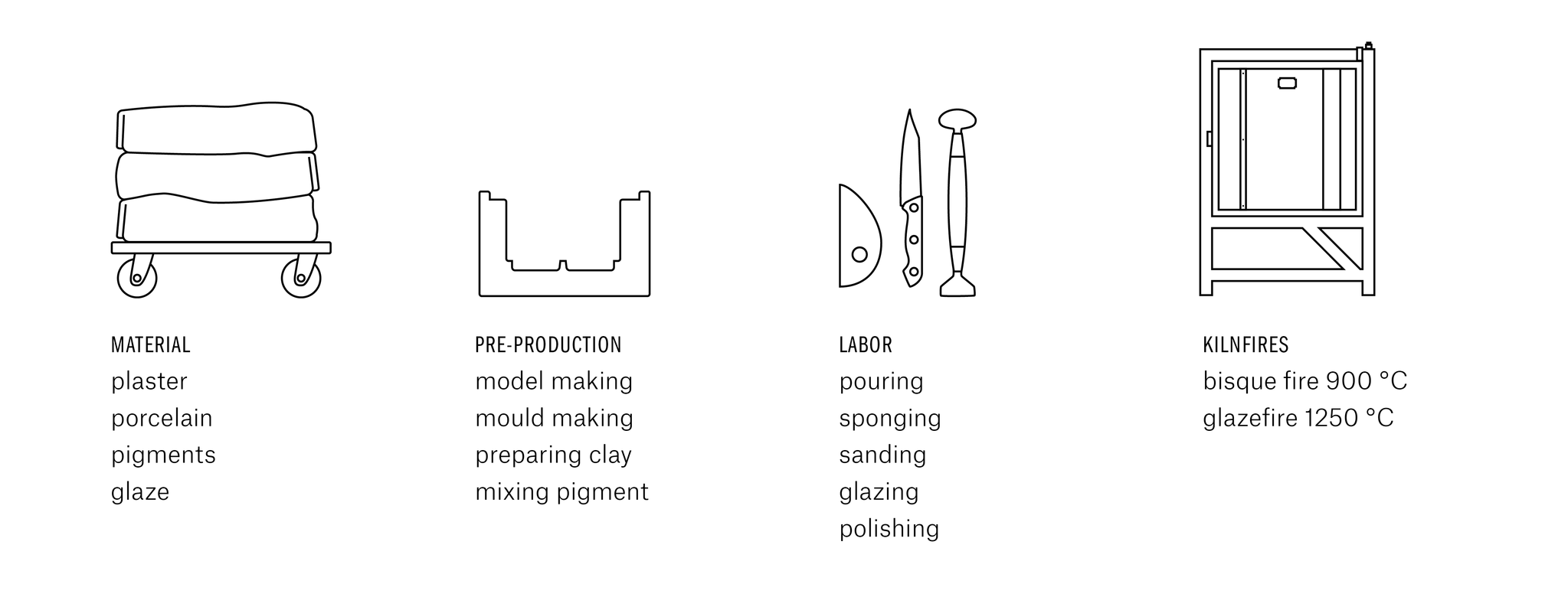
In my second year of school I learnt how to make moulds. I fell in love with ceramics from this moment.
This process gave me the opportunity to recreate the same piece again. Starting with a model I can create severals moles.
The next step is mixing the clay, this takes up to 3 hours. Finally I add the pigments. Every step completed by hand in my Amsterdam studio.
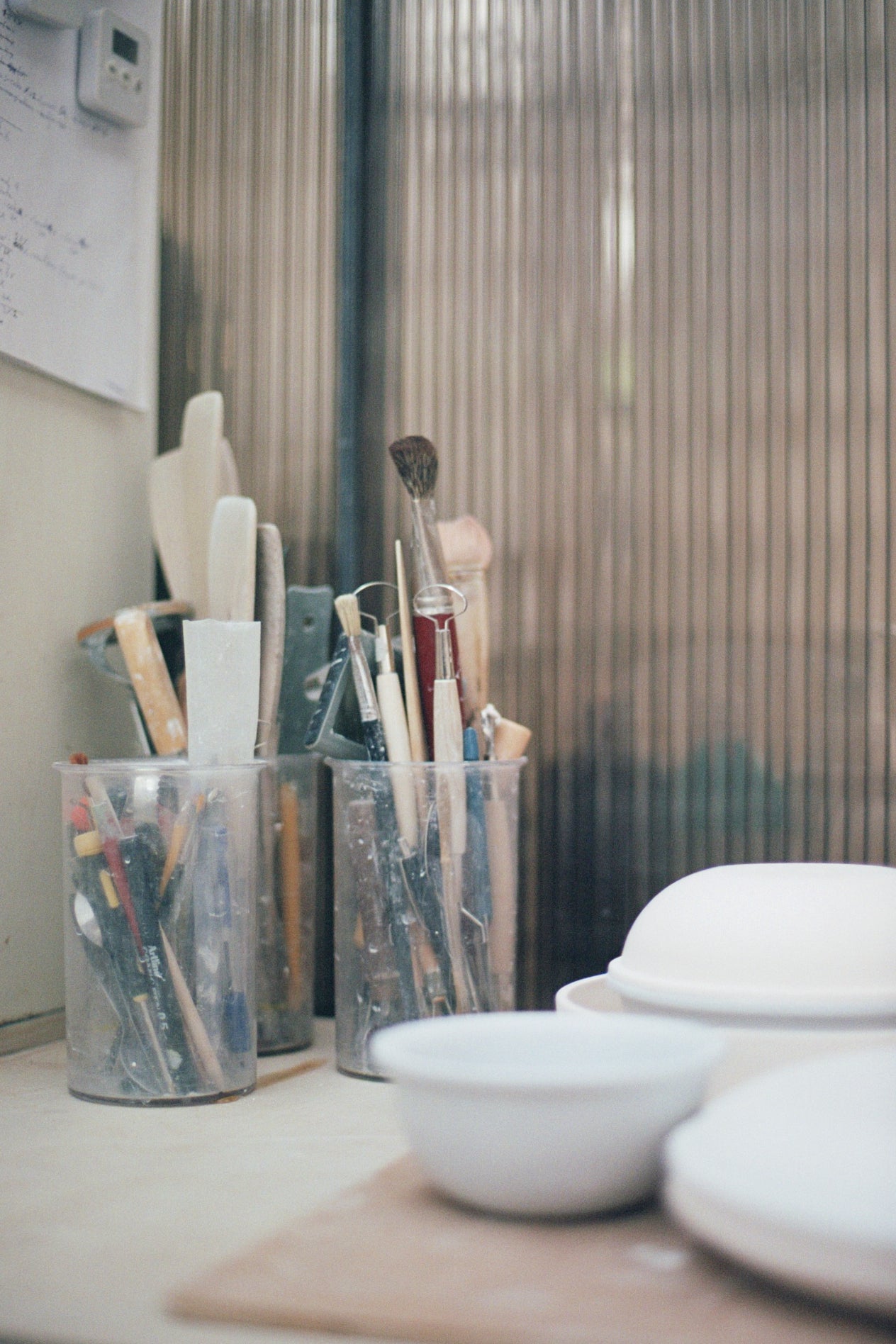
The end result is only visible after every step of the process is completed. Continous focus is key to success here.
Sponging is the most fulfilling step for me. The clay is still raw & at its most fragile. Moving the we sponge over the clay gives the item the perfect, smooth finish. The appearance of the item can still change as squeezing too hard could break the piece.
After sponging the pieces are ready to be fired for the first time. This step is called bisque firing. It is important the porcelain is bone dry to prevent cracks. A bisque fire takes 1.5 days.
Firing at 900 degrees changes the porcelain bound yet porous ceramic. This is ideal for glazing.
Finally, it's time for the high fire at 1250 degrees. Each pieces must be clean from dust & stacked 1cm apart. During this step the porcelain experiences several chemical reactions. After firing they need to cool slowly. Bisque firing takes 2 days.
Opening the kiln is never a surprise, it is proof that you completed each step properly. It is the most exciting moment.